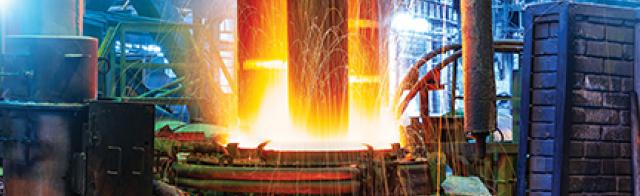
Challenge for modern steel making
Foamy slag is at the heart of modern steel making in electric arc furnace (EAF) process. The foaming helps to shield refractories from arc plasma, stabilises the arc and helps to increase the power input and energy efficiency, reduces N2 pick-up, improves productivity, and chromium recovery in stainless steel melting.
The generation of the early liquid slag is a prerequisite for foaming. The stability and control of foaming height is critical assisted by reactions generating small gas bubbles and suitable slag properties to keep the bubbles as stable foam. The slag viscosity, surface tension, and presence of suspended second phase particles are critical slag properties to sustain foaminess.
Product quality
Lime and dolime quality attributes such as chemical composition and loss on ignition influence the amount of lime, time, and energy required to attain slag properties critical for foaminess. For example, any additional impurities from lime including SiO2, is a burden to the process, needing extra amount of lime and alter slag properties and volume.
Lime injection clearly helps to sustain the foaminess through controlled process, flow, and timings of addition. Lime injection performance however depends on right selection of lime properties for a type of injection system and expected flow rates. The lime needs to meet some further stringent requirements such as particle size distribution to enable high and reliable flow control.
We make sure our customers get the most suitable high-calcium soft-burnt lime and dolime products to build on their foaming slag practice. At Carmeuse, we perform additional tests and even simulate customer’s conditions and layout to ensure smooth and reliable flow of lime.
At Carmeuse, we strive to help our customers in achieving and sustaining foaminess so to enable them in improving productivity, cost, metallic yield, quality, safety, and better environment in the steel shop.
Lime injection technology helps in:
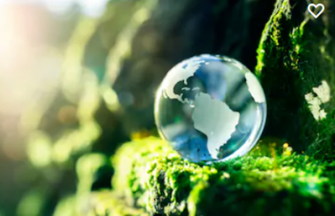
It generally provides a closed circuit environment that minimizes the risk of human exposure to lime, while helping to reduce the cost related to safety by minimizing lime dust in the shop. It also significantly improves the working environment, while reducing the energy cost and disposal cost of dust. The pneumatic transport of lime fines through a closed system enables 100% efficiency into the metal bath.
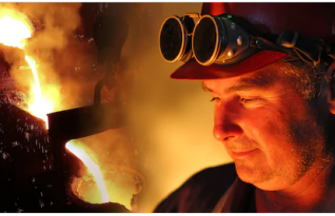
Current EAF slag practices allow early and sustained foaming due to lower basicity ratios having sufficient MgO levels, enabling faster dissolution of lime through lime injection fines into the slag/metal interface. Another important feature of lime injection is the enabling of slag foaminess during the last part of liquid steel superheat phase when the foamed slag tends to lose such status An intensive lime and dolime fines injection improve slag viscosity and thermal efficiency of the process, leading to a better heat transfer from arc to molten metal.
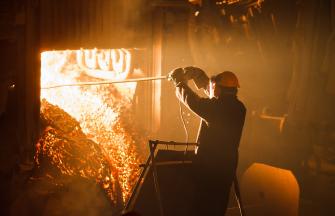
The coherent jet of lime injection, shrouded with oxygen, helps lime directed into the slag metal interface, minimizing the chance of any lime particles being lost to de-dusting systems. This jet enables near to 100% utilization of lime injection, compared to about 80% with traditional addition.
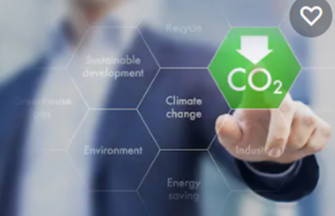
Lime injection brings significant cost benefits from reduction in lime consumption to process benefits including but not limited to –
- reduce erosion of the refractories,
- less metal droplets loss to slag,
- lower amount of slag generation helping to save on FeO loss in slag,
- less melting power, reduced electrode consumption,
- better efficiency of both oxygen and fuel gas being injected.
It is critical to match the lime characteristics (attributes) with the technology enabling a smooth and consistent flow rate of lime. There is a possibility to use fines created in the captive lime plant subject to a complete feasibility analysis and implementing recommended changes. Lime injection in steel making process helps to reduce significant costs, improve quality, and is environment friendly.
CARMEUSE EXPERTISE
INJECTION PILOT FACILITY
Carmeuse’s fully operational lime injection pilot system is capable of testing and comparing current or potential lime injection materials in multiple configurations. This modernized system is equipped with an HMI as well as a remote/pulpit control. The system is completely equipped with a screen box, a feed hopper, capacity injection vessel, customized piping configurations and a back pressure simulator to simulate the pressure that an electric arc furnace would put on a lime injection system. This back pressure simulator can be adjusted to increase or decrease the pressure observed on the system. The most aggressive configuration has over 80 m length of 8 cm diameter piping, eight 90-degree elbows and a vertical run of over 10 m.
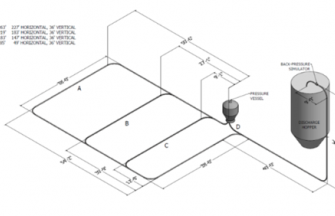
Why CARMEUSE is the most suitable for this cooperation?
- Carmeuse has positioned itself as the KNOWLEDGE LEADER IN LIME INJECTION SYSTEMS that are becoming the proven technology for the modern steel maker.
- Being CUSTOMER FOCUSED is a core value at Carmeuse, helping to educate steelmakers about this contemporary steelmaking application. We continually work with customers to identify and solve problems that might be encountered while using lime injection systems specific to their steel making process.
- Carmeuse EXPERTS are available to advise on enhancing performance and provide technical solutions.
- Carmeuse innovation department is continually working to DEVELOP NEW INNOVATIVE PRODUCTS and improve upon available products for customer’s applications. Our innovation facilities in Europe and North America are working very closely but independently meeting demands of local markets.
- We understand the importance of reliability of injection systems, maximum possible flow rates, and controls on the entire process. Carmeuse is in PARTNERSHIP with leading technology suppliers.
- Carmeuse is keen to work in partnership and support your INVESTMENT needs to install lime injection in your furnace.
CARMEUSE is a GLOBAL LEADER and EXPERT in providing the optimum lime products customized to your applications in steel industry covering agglomeration, sintering, and steel making processes. Carmeuse pioneered developing products and technology for lime injection in Electric Arc Furnaces, Basic Oxygen Furnaces, and dosing in sinter plant. Our commitment and leadership in injection technology is backed with huge investments in R&D, injection pilot facility at Millersville, Ohio and a strong customer reference list.
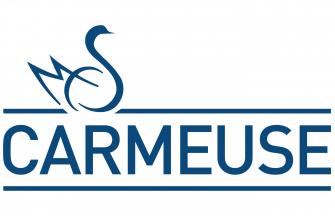